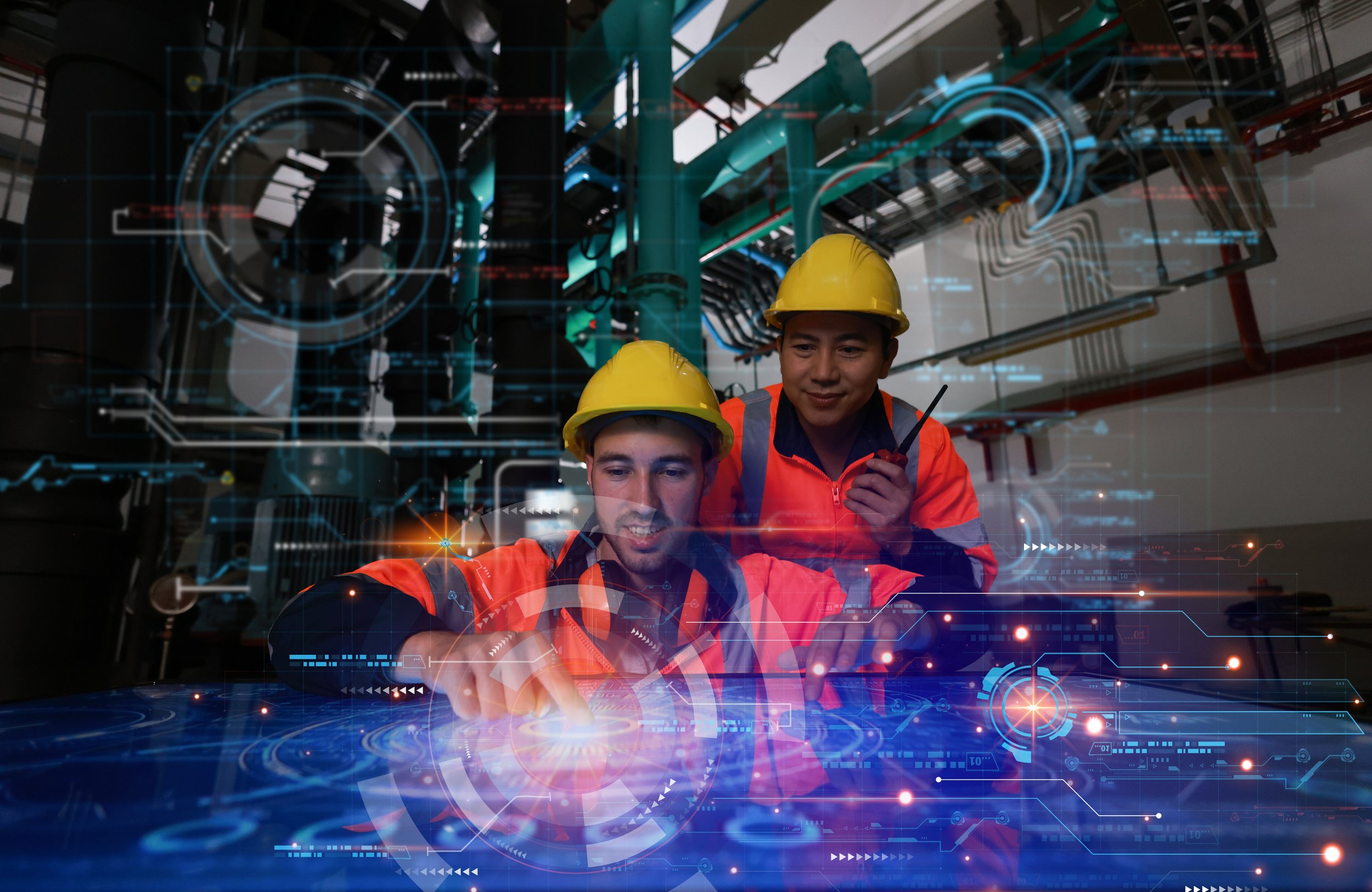
E8 Ventilation Diagnostics Sdn. Bhd.
Testing, Examination and Troubleshoot Industrial Ventilation Systems
Why Testing and Assessment ?
Testing and Assessment has various purposes ranging from identification and quantification of occupational and environmental hazards, performance monitoring of control integrity as apart of predictive maintenance checks, collection of data for system degradation trouble shooting, commissioning and baseline assessment, compliance monitoring and other specifics objectives.
The most important part at this stage is to derive the objective of the testing and assessment very clearly. Once the objective is define, the parameters involved need to be derived. The derivation of the objection and the testing parameters will enable accurate testing and assessment strategies. The range of testing and monitoring objective can range from random test, baseline establishment, periodic check in comparing to peak or baseline condition, risk evaluation, control integrity check and trouble shooting measures. The test can be ranging from industrial hygiene monitoring, environmental impact evaluation, system efficiency assessment. As from the aspect of ventilation system it can range from duty point and fan-system curve performance checks, periodic check on performance within peak and low limit (allowable limits), motor power optimisation, system static pressure increase and etc.
The selection of the testing and assessment methods is best to be done based on any acceptable standard references. These methods can be obtained easily based on the objectives via reference to the specific parameters. For instance, in the testing and assessment relating to industrial hygiene, American Conference Governmental Industrial Hygiene (ACGIH) Methods can be referred to its specific manuals which are easily available for the ACGIH websites or references material. Similarly, Industrial ventilation method approaches can be made from reference sources of American Society of Heating, Refrigerating and Air-Conditioning Engineers (ASHRAE).
How we can help you.
Industrial Hygiene Monitoring
The tenets of industrial hygiene spells out that anticipation, recognising of hazards are the most important part in evaluating its hazard. The quantified hazard magnitude will be used to evaluate the risk using the specific criterion based on the concerning hazard. Upon completing of the risk evaluation, the control integrity is to be established based on the quantified numbers. We provide the comprehensive data for the evaluation of the risk and will package the formation of the controls. The ranges of the test could range from objective as simple as random checks, creating concrete hazard generation data for risk evaluation simulation, risk evaluation test, preliminary data for system design, control integrity checks, evaluation change of management and etc. Hazard identification process is the fundamental step in recognising and anticipating the occupational stressors which ranges from heat, humidity, light, noise, chemical. microbiological and ergonomic. Proper definition of these stressors related to the occupational settings must be done as to derive the most accurate control measure in ameliorating the risk.
The list of IH testing and monitoring works we provide are :-
Chemical Health Risk Assessment
Chemical Exposure Monitoring
Heat Stress Assessment
Lux Monitoring
Ergonomics Assessment
Noise Risk Assessment
Audiometry
Airborne hazards qualitative identification at the source
Airborne hazards qualitative identification at the point of dispersions / sensitive recipient / ground level concentration
Chimney / Stack Emission Monitoring
The last components of the industrial local exhaust ventilation system discharges captured and diluted airborne stresses ranging from chemical, biological and physical stressors. Stressors or contaminant with low concentration range may be directly discharges and high ranges may be going through the air cleaning device. The emission which is at the final point of exit must be vertically discharge with momentum to create buoyancy for formation of effective stack height, forming plume rise and dispersion at the elevated level not affecting ground level concentration. The dispersion trajectory which will be elevated mostly will drop the significant level of any residual concentration from high to low making it homogeneous with the air eventually. Chimney emission monitoring is to be conducted to evaluate this functionality. Chimney emission monitoring can also serve as apart of predictive maintenance monitoring of a ventilation system as the system flow rate and the emission quality will be within the pattern of the baseline condition unless the system is undergoing deterioration or the process has undergoing significant changes in airborne contaminant generation.
Chimney / Stack Emission monitoring can be done with these objectives :-
Baseline isokinetic emission testing to determine the baseline concentration of the aerosols (particulate matter) airborne hazards from process / upon air cleaning device abatement
Baseline emission testing to determine the baseline concentration of the vapour and gaseous type of airborne hazards from process / upon air cleaning device abatement
Periodic isokinetic and emission testing for both aerosols and vapour-gaseous to evaluate the changes in emission quality in comparison to system efficiency
Evaluate vertical discharge performance for buoyancy adequacy (efflux velocity) in forming effective plume rise
Air cleaning device performance assessment in quality of permeated vertical discharge
Industrial ventilation commissioning, baseline, periodic and troubleshooting testing and assessment
A ventilation system which comprises of General Ventilation and Local Exhaust Ventilation System runs on basic fundamentals of pressure variance churning air displacement and driven by power motored running at certain speed to meet the duty point it is designed for. Once a system is design and constructed the commissioning process will be undertaken to set the condition as per the process requirements. Upon creating a balance between ventilation system functionality without hindering process flow, the baseline date which is the peak performance of the system will be assessed and recorded as the baseline date. This baseline data combine with the lower limit will serve as the operation performance acceptable range. Deterioration of performance outside the acceptable range will trigger the need for corrective maintenance.
The list of Industrial Ventilation System testing and monitoring services we undertake are as follows :-
Testing and Commissioning during Wet and Dry Run
Baseline Testing of LEV and GV System
Testing and Balancing
Performance Monitoring, Preventive Maintenance and Predictive Maintenance.
Troubleshooting Ventilation Systems
Operator Skills and Training
Bearing, shaft, pulley, motor replacement and maintenance
Impeller On site balancing, Impeller factory balancing
Contact us.
Have questions about our solution options? Talk with an E8 Group expert to learn how we can support your needs.
Talk to us
sales@e8group.com.my
Tel : 03 80248148 / 6149
Fax: 03 80246148
Southern Office
No 04-09, Blok A, Pusat Perdagangan Ekoflora, Jalan Ekoflora 7/3, Taman Ekoflora, 81100, Johor Bahru, Johor. Tel : 01 23078108
Subang Office
19-1, Jalan USJ 21/6, 47630. Subang Jaya. Selangor.